Kanigen LP
Chemical nickel plating
Coating definition
Coating definition
Electroless nickel plating is a deposition process using
solution This aqueous process enables a nickel-phosphorus alloy to be deposited on all common metals used in the manufacture of machine parts, without the need for an external power supply. Its remarkable properties have made it a key player in the field of functional metal deposition for many years.
The Kanigen® process, in which Kanigen stands for KAtalytic NIckel GENeration, was developed by G.A.T.X. (General American Transport Corporation) in the late ’50s. This is the name of the original electroless nickel plating process. Atela SA began its activity by purchasing the Kangien® license for Switzerland.
The main characteristics of the KANIGEN® deposit are homogeneity and controllable thickness, gloss, density and non-porosity of the coating. They can be applied to all common construction metals, including low- and high-alloy steels, non-ferrous metals (copper, brass, bronze, inconel, etc.) and aluminum, titanium and magnesium alloys.
Non-conductive substrates such as plastics, glass, ceramics and semiconductors can also be coated using a suitable preparation procedure.
Type of deposit
KANIGEN® deposits are produced in three variants, each with a different phosphorus content in the NiP alloy and different properties:
Properties
to ISO 4527
|
KANIGEN HP High phosphorus
|
KANIGEN MP Medium phosphorus
|
KANIGEN LP Low phosphorus
|
Electrolytic nickel |
---|---|---|---|---|
Chemical composition | > 10% wt. Phosphorus | 5 – 9% wt. Phosphorus | 1 – 4% wt. Phosphorus | Classic structure |
Structure | Amorphous (metallic glass) |
Microcrystalline | Microcrystalline | Crystal |
Bath capacity | 2000 x 790 x 1300 mm | 1150 x 670 x 1800 mm | 1150 x 670 x 1800 mm | |
Melting point | 875°C | 890°C | 910°C | 1’452°C |
Density | 7.9 | 8.2 | 8.5 | 8.9 |
Expansion coefficient |
13 x 10 – 6 / °K at room temperature
|
13 x 10 – 6 / °K at room temperature | 13 x 10 – 6 / °K at room temperature | |
Thermal conductivity (W/cm x K) |
0.044 – 00.57 |
~ 0.7
|
~ 0.7 | 0.95 |
Electrical resistivity (µOcm) |
110 | 72 | 30 | 6.8 |
Wear resistance after line. Therm. 290°C 5h (Taber index)
|
8 | 6 | 3 | 14 |
Magnetic susceptibility |
Amagnetic
|
Slightly magnetic | Magnetic | Magnetic |
Hardness (without Therm line) |
~ 520 HV 0.1
|
~ 580 HV 0.1
|
~ 650 HV | 200 HV |
Hardness (with trait. Therm 290°C 5h)
|
~ 900 HV 0.1 | ~ 900 HV 0.1 | ~ 900 HV 0.1 | 150 – 200 HV 0.1 |
Elasticity (unhardened deposit) |
~ 2% |
~ 0.3%
|
~ 0.1% | 18% |
Features
Features
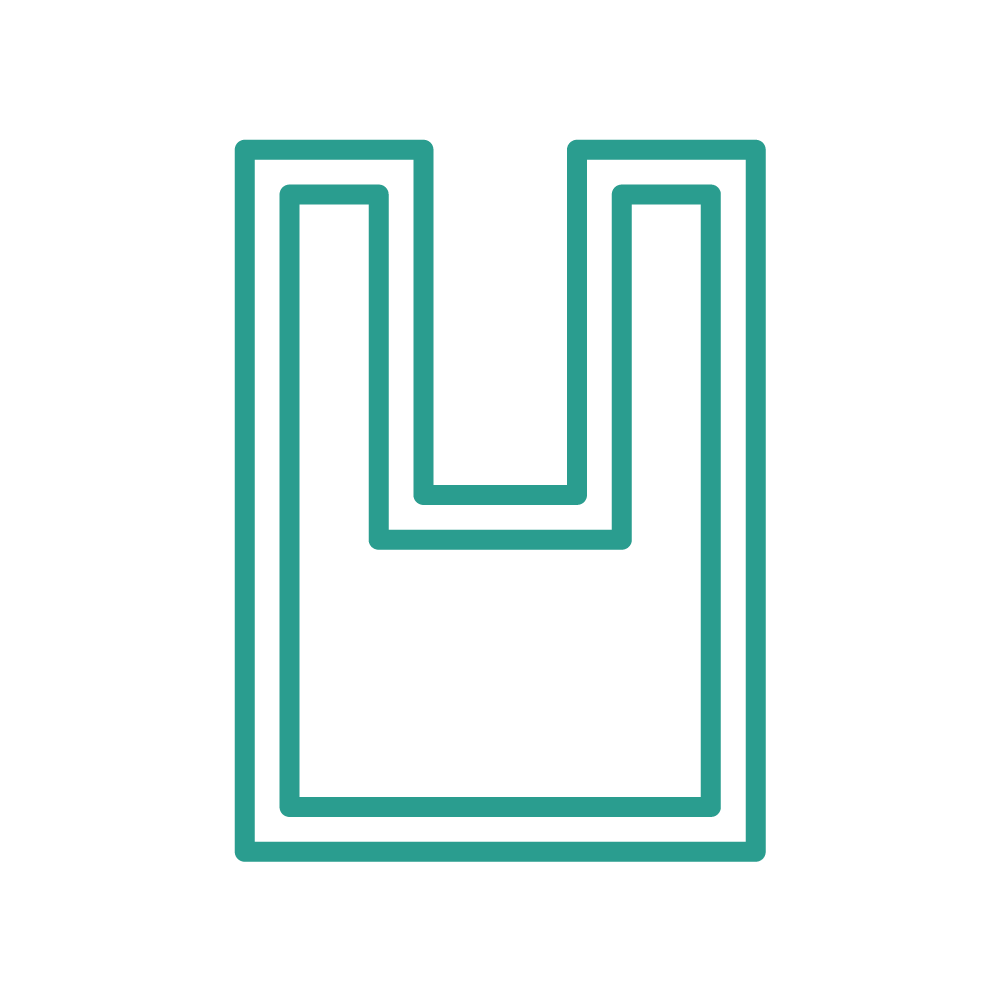
Thickness uniformity
Unlike the electrolytic process, which is limited in thickness in hollow parts and produces extra thickness on the most exposed parts of a component, electroless nickel plating produces a deposit of uniform thickness over the entire surface of the part, even if its shape is highly profiled.
This remarkable property reconciles mechanics with surface treatment.
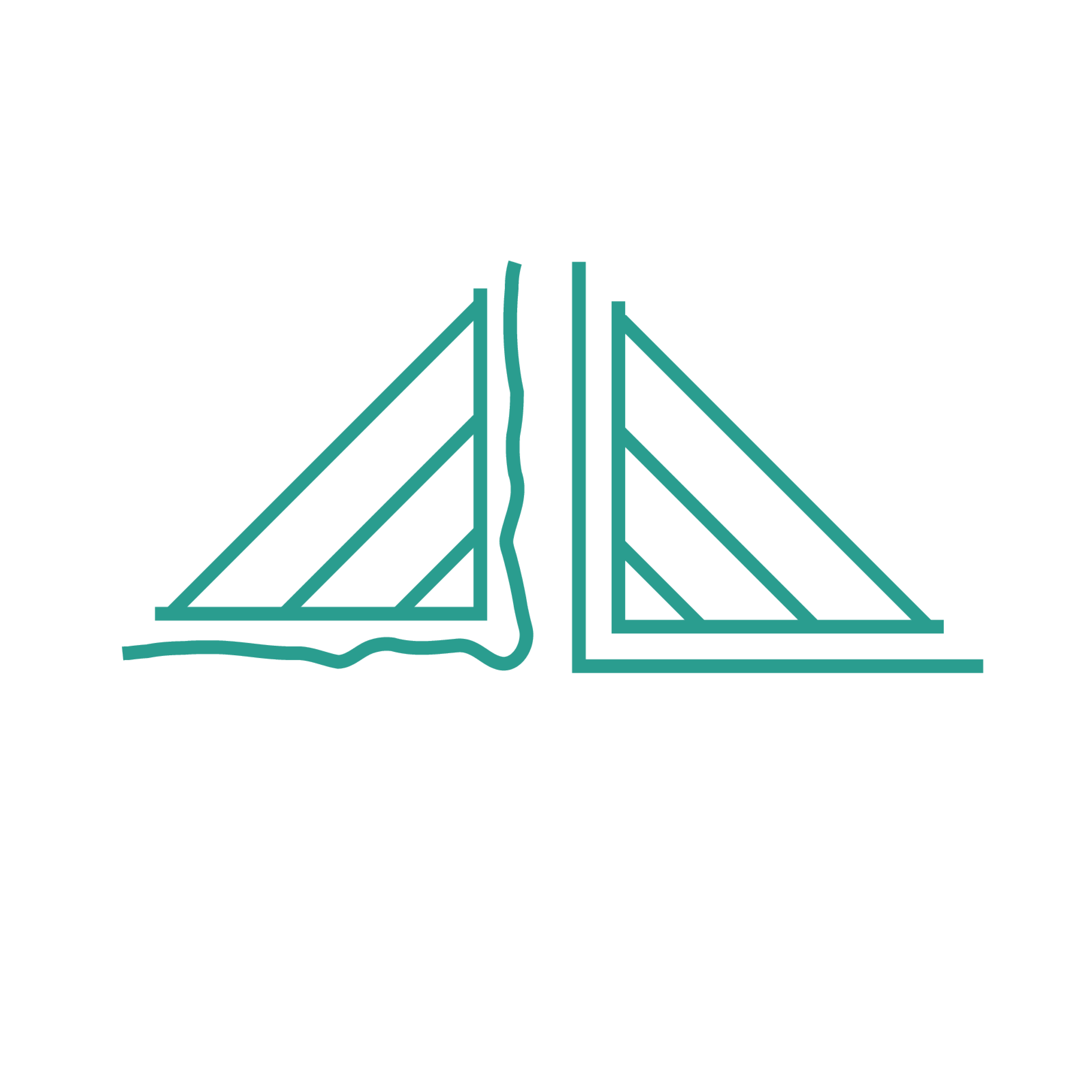
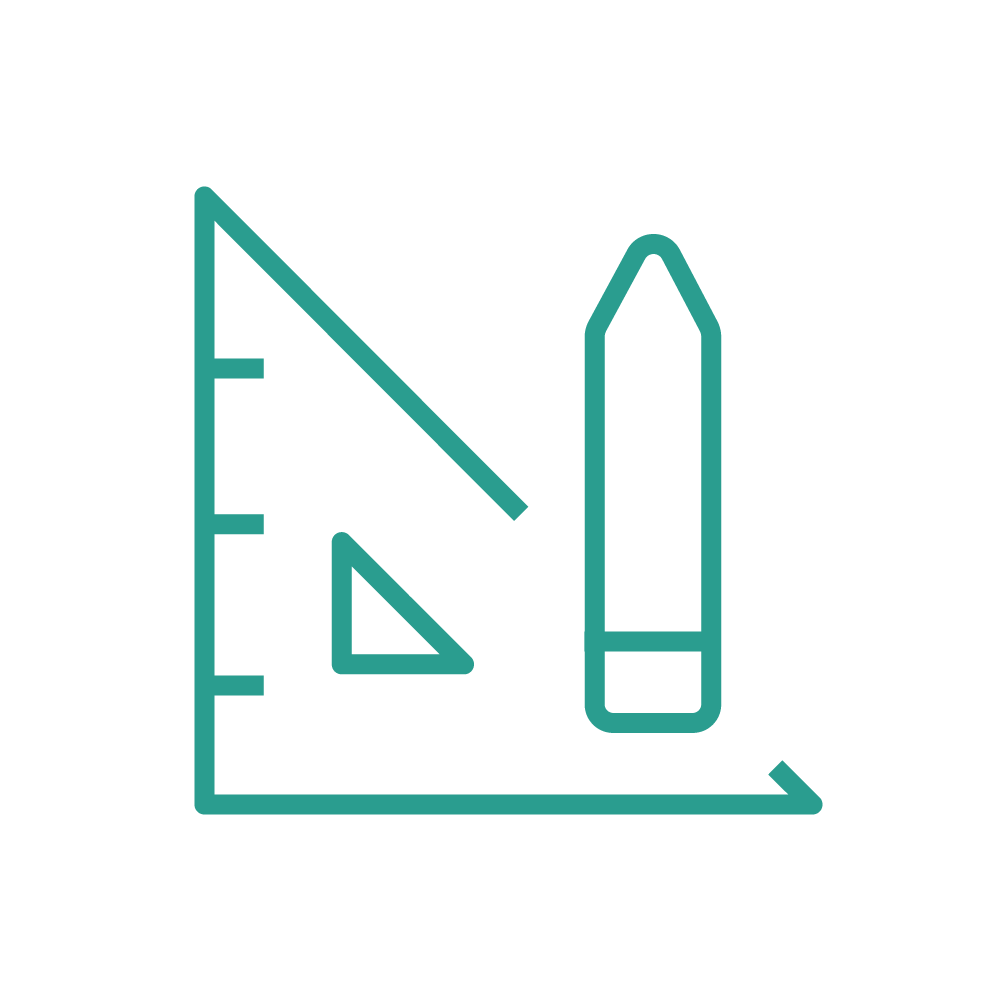
Thickness accuracy
Very high precision can be achieved with electroless nickel plating. We guarantee a micro-lending thickness of +7- 10%.
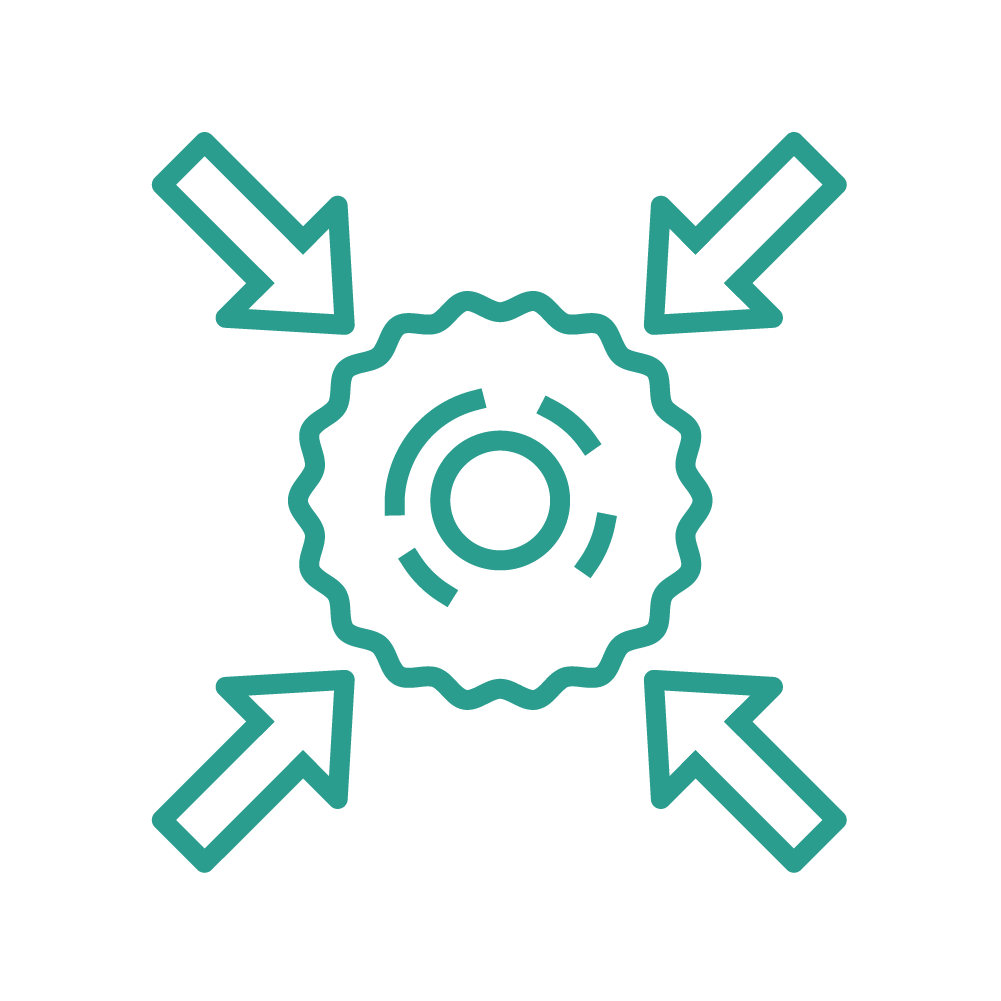
Deposit recovery power
Reduced weight and assembly size The most inaccessible parts of a component can be coated, provided the surfaces are in contact with the bath. This makes it possible to coat parts with complex geometries.
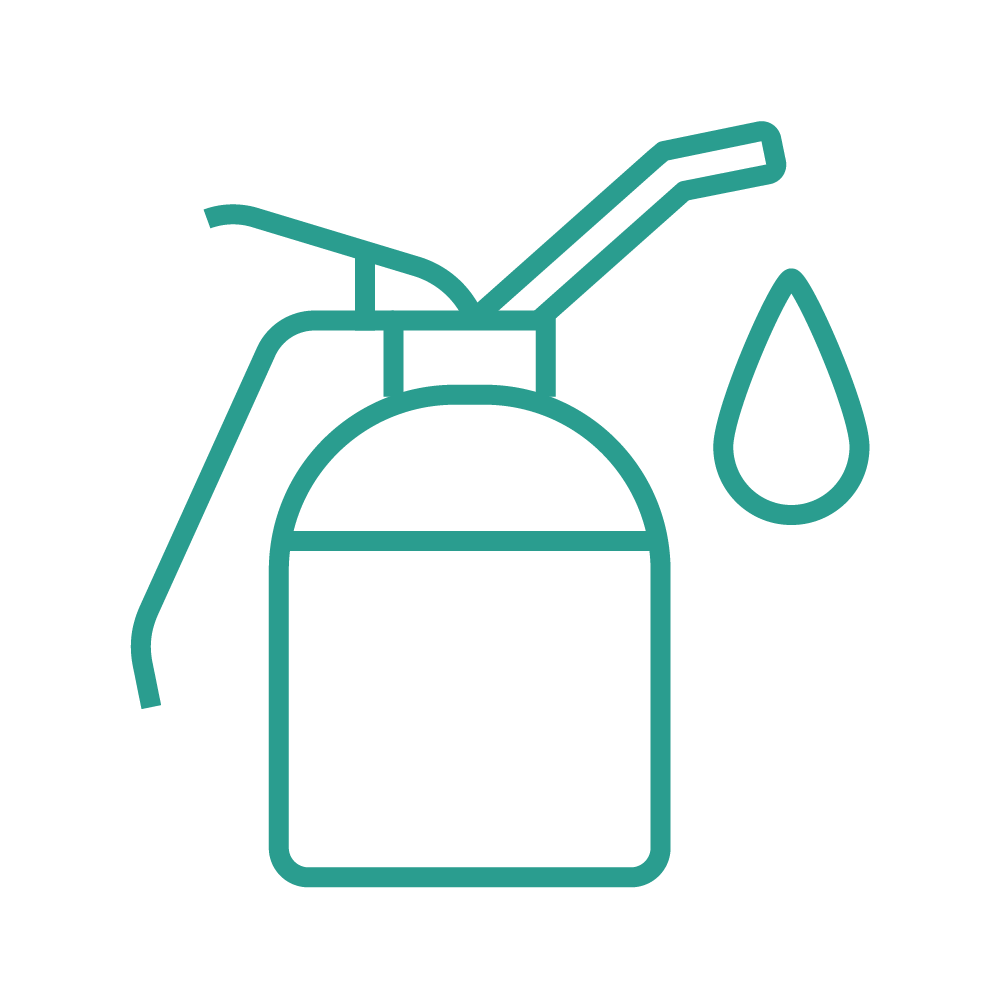
Hardness
From 500-550 HV 0.1 in its non-heat-treated state (raw bath), hardness can be increased to 1100 HV 0.1 by heat treatment for one hour at 400 C or 5 hours at 290 C.
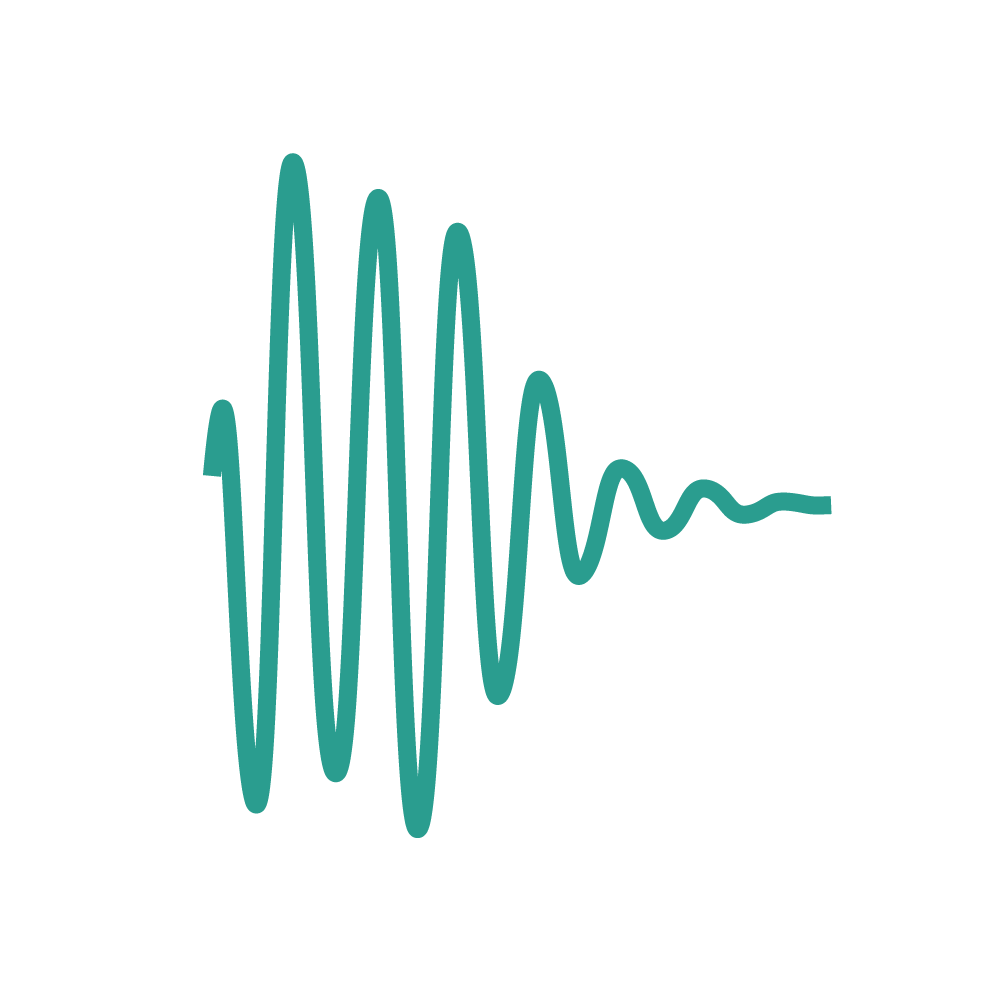
Solderability
Electroless nickel enables soft soldering and brazing. It can be used to make materials such as aluminum alloys, stainless steel and inconel weldable.
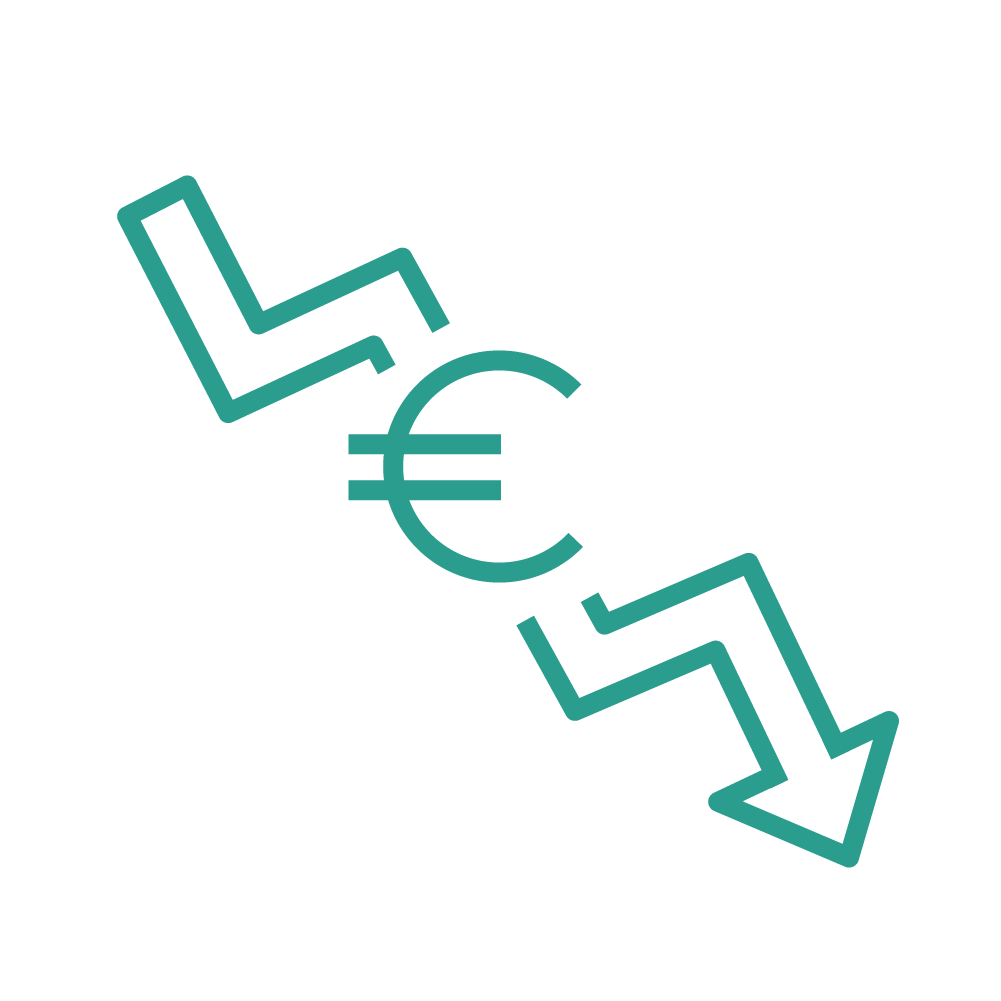
Wear resistance
A heat-treated KANIGEN deposit is up to 5 times more wear-resistant than an electrolytic nickel deposit according to the Taber index.
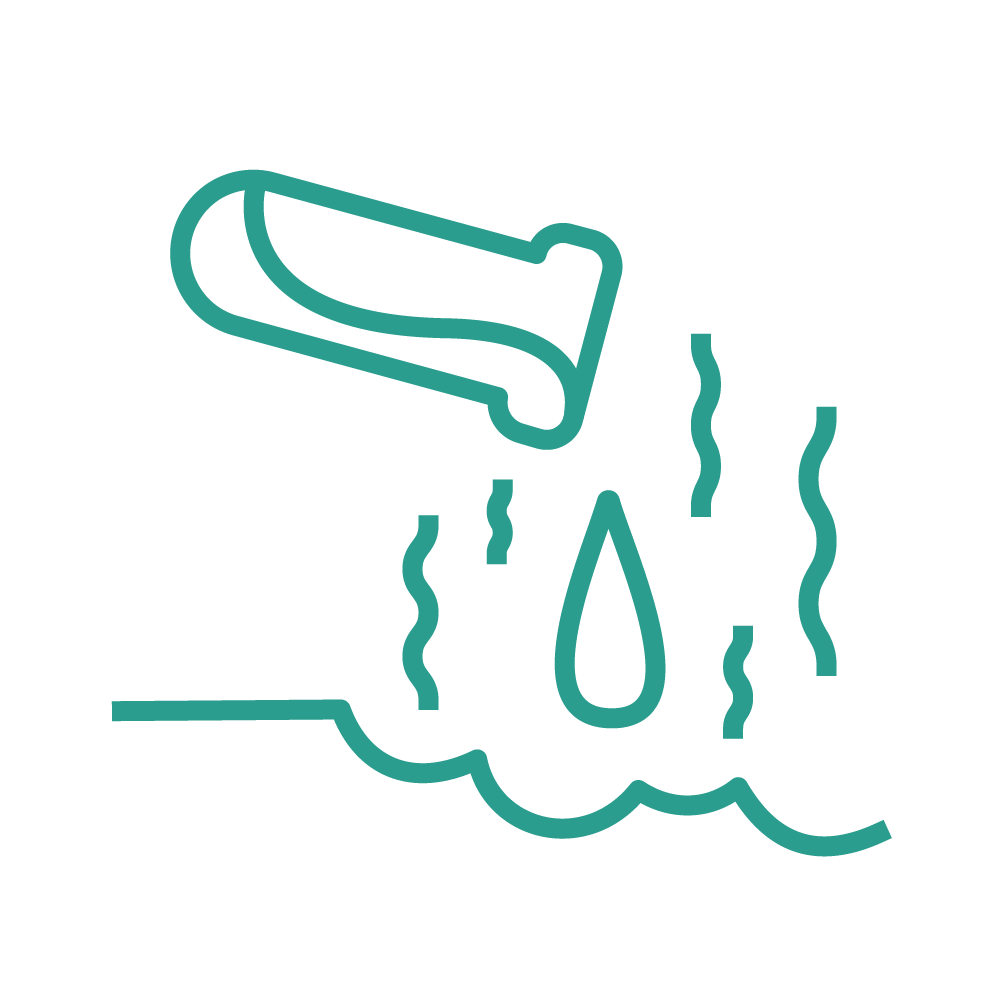
Corrosion resistance
A heat-treated KANIGEN deposit is up to 5 times more resistant to corrosion than an electrolytic nickel deposit according to the Taber index.
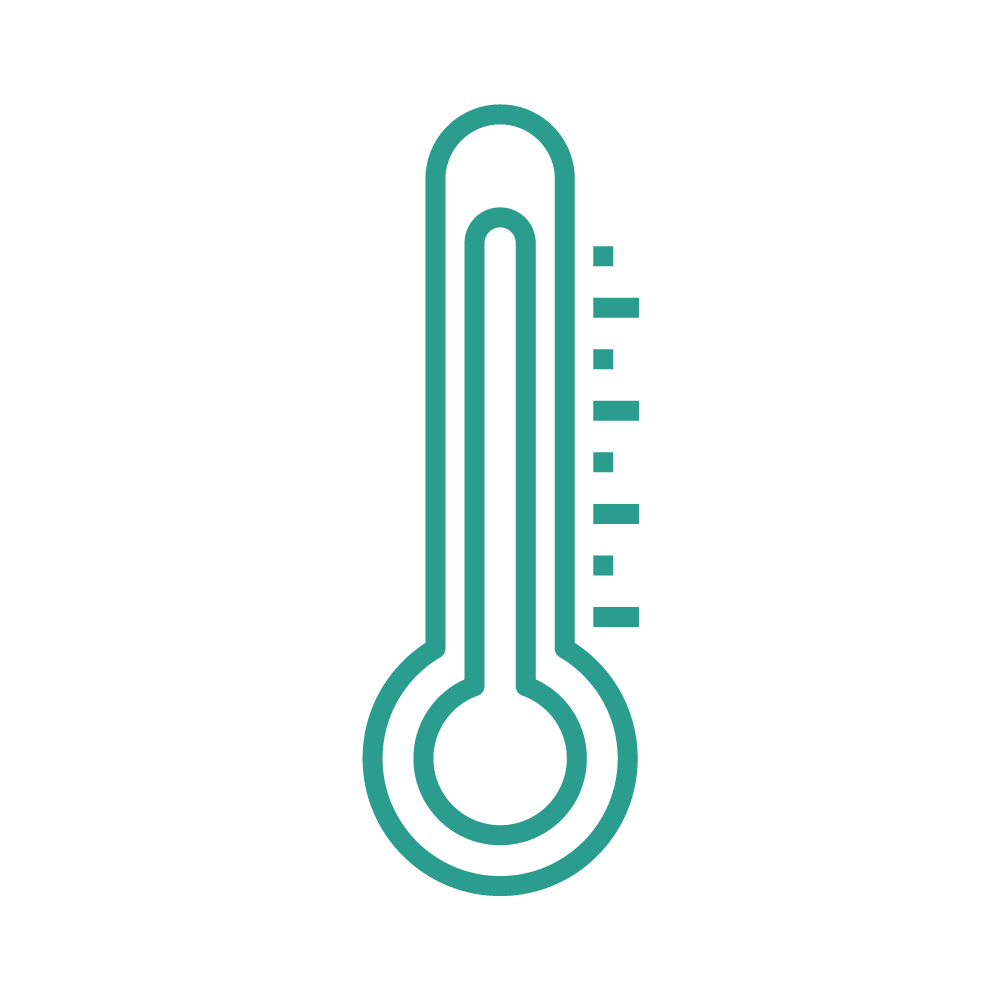
Influence of thermal treatments
Heat treatments affect the properties of KANIGEN deposits in different ways:
AT 200°C :
Heat treatment at approx. 200°C helps to relieve internal stresses and improve adhesion to the substrate, particularly on aluminum alloys.
240°C to 400°C :
From 240°C up to 400°C, KANIGEN HP deposits harden by precipitating nickel phosphides in Ni3P form.
400°C :
From 400°C onwards, recrystallization and grain coarsening occur, leading to a gradual drop in hardness.
AT 600°C :
At 600-650° C, Ni-Fe inter-diffusion between the deposit and the substrate occurs at the interface of steel or cast-iron substrates, increasing adhesion to such an extent that the deposit can be considered as melted onto the workpiece. It is also at these temperatures that the KANIGEN deposit acquires its best resistance to wear and abrasion.
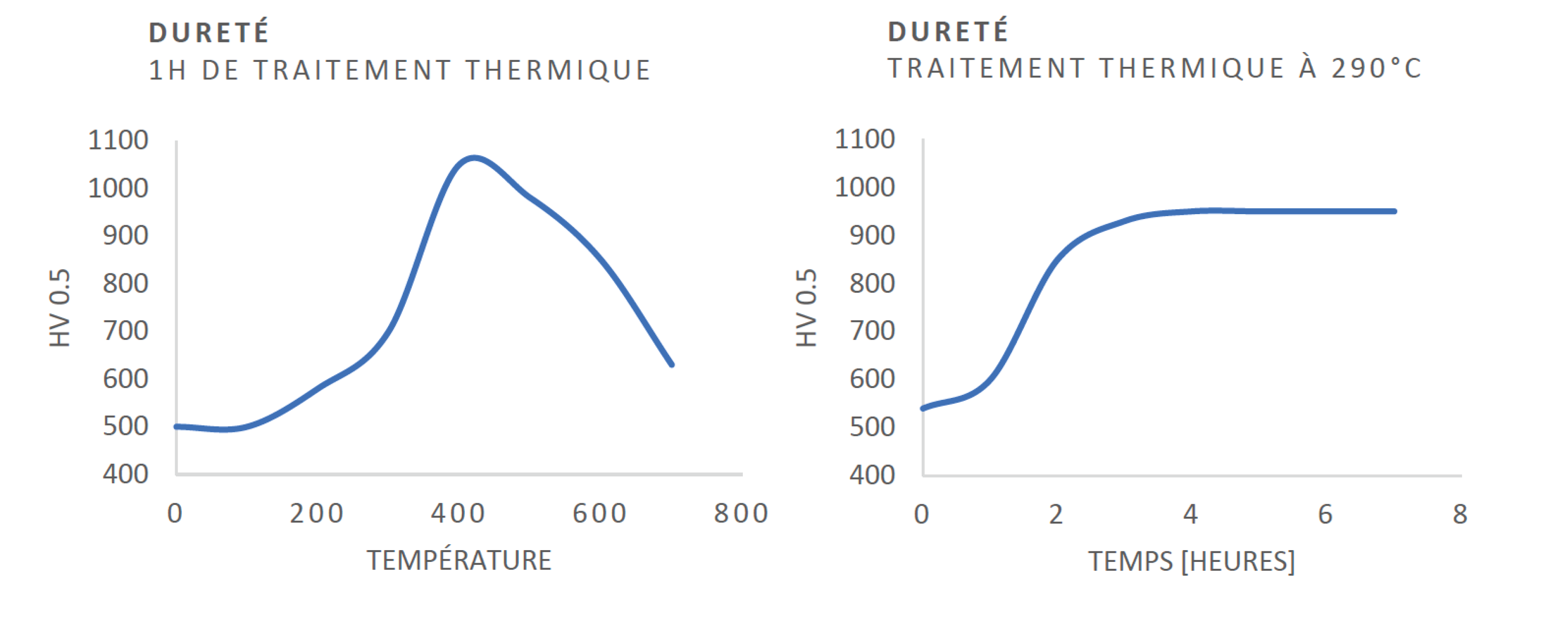