Dianip G
Increased coefficient of friction
General
Increasing the coefficient of friction of a surface can be very useful in certain areas of the machine industry, such as gripping or braking systems, or locking a moving part in a defined position.
With DIANIP G, ATELA offers a high-friction coating for improved torque transfer. By embedding diamond grains of defined size in an electroless nickel matrix, the surface roughness is chosen to transmit high force torques without damaging the driven part.
Application examples
- Increased chassis rigidity (Formula 1, Moto GP, Satellites)
- Fixing precision mirrors (telescopes, lithography)
- Reduced machining costs (machining jaws)
- Sharpening (Sharpening guns, sharpening stones)
- Lock (Safety brakes)
- Torque transmission if friction spacers cannot be used (test bench, steering column or articulated arm locks)
- Torque or weight sensors
To name but a few.
Features
Thanks to their precise, even roughness, DIANIP G coatings significantly improve the tribological properties of the parts to which they are applied. Treated parts enhance the efficiency of drive, braking and gripping systems.
DIANIP G consists of a chemically deposited Nickel-Phosphorus alloy matrix in which fine diamond particles of well-defined, highly uniform size are embedded. The coefficient of friction thus induced will depend essentially on the size of the diamond grains incorporated.
By incorporating diamond grains with an average size ranging from 25 to 50 microns, the abrasive properties are such that rubbing against them produces such an aggressive, rough surface that it’s ideal for sharpening tools and knife blades.
With a finer diamond grain size, between 10 and 13 microns, our coatings are satin-finish to the touch and are perfect for training without slipping and therefore without unnecessary heating and energy loss.
TECHNICAL PROPERTIES
Property | DIANIP C2 | DIANIP G10 | DIANIP G13 | DIANIP G25 | DIANIP G35 | DIANIP G50 |
---|---|---|---|---|---|---|
Functions |
Abrasion, wear and friction resistance
|
Roughness, Grip, Training | Roughness, Grip, Training | Roughness, Grip, Training | Sharpening | Sharpening |
Particle type |
Single-crystal diamond
|
Single-crystal diamond | Single-crystal diamond | Single-crystal diamond | Single-crystal diamond | Single-crystal diamond |
Grain size (median) |
2 µm
|
10 µm
|
13 µm
|
25 µm
|
35 µm
|
50 µm |
Fill-factor | N/A |
8 – 55%
|
8 – 55% | 8 – 55% | 8 – 55% | 8 – 55% |
Hardness of PIN matrix |
400 – 600 HV 0.1
|
400 – 600 HV 0.1 | 400 – 600 HV 0.1 | 400 – 600 HV 0.1 | 400 – 600 HV 0.1 | 400 – 600 HV 0.1 |
PIN matrix thickness |
from 3 to 80 µm
|
from 6 to 12 µm
|
from 8 to 12 µm | from 15 to 19 µm | from 9 to 27 µm | from 28 to 36 µm |
Total thicknessof DIANIP coating | idem |
15μm ± 10μm
|
17.5μm ± 10μm | 30μm ± 10μm | 45μm ± 15μm | 65μm ± 25μm |
Bath capacity |
980 x 630 x 1000 mm
|
400 x 400 x 500 mm
|
400 x 400 x 500 mm | 400 x 400 x 500 mm | 800 x 400 x 500 mm | 800 x 400 x 500 mm |
Coefficient of friction(µsvs. steel) | 0.4 – 0.6 | 0.55 – 0.80 | 0.55 – 0.80 | 0.55 – 0.80 | 0.55 – 0.80 | 0.55 – 0.80 |
Melting point |
875 to 890 °C (pure nickel: 1455 °C )
|
875 to 890 °C (pure nickel: 1455 °C ) | 875 to 890 °C (pure nickel: 1455 °C ) | 875 to 890 °C (pure nickel: 1455 °C ) | 875 to 890 °C (pure nickel: 1455 °C ) | 875 to 890 °C (pure nickel: 1455 °C ) |
Melting temperature |
Up to 300°C
|
Up to 300°C
|
Up to 300°C
|
Up to 300°C
|
Up to 300°C
|
Up to 300°C
|
Adhesion to steel |
30 to 60 Kpsi
|
30 to 60 Kpsi | 30 to 60 Kpsi | 30 to 60 Kpsi | 30 to 60 Kpsi | 30 to 60 Kpsi |
Elasticity (uncured deposit)
|
0.7%
|
0.7%
|
0.7%
|
0.7%
|
0.7%
|
0.7%
|
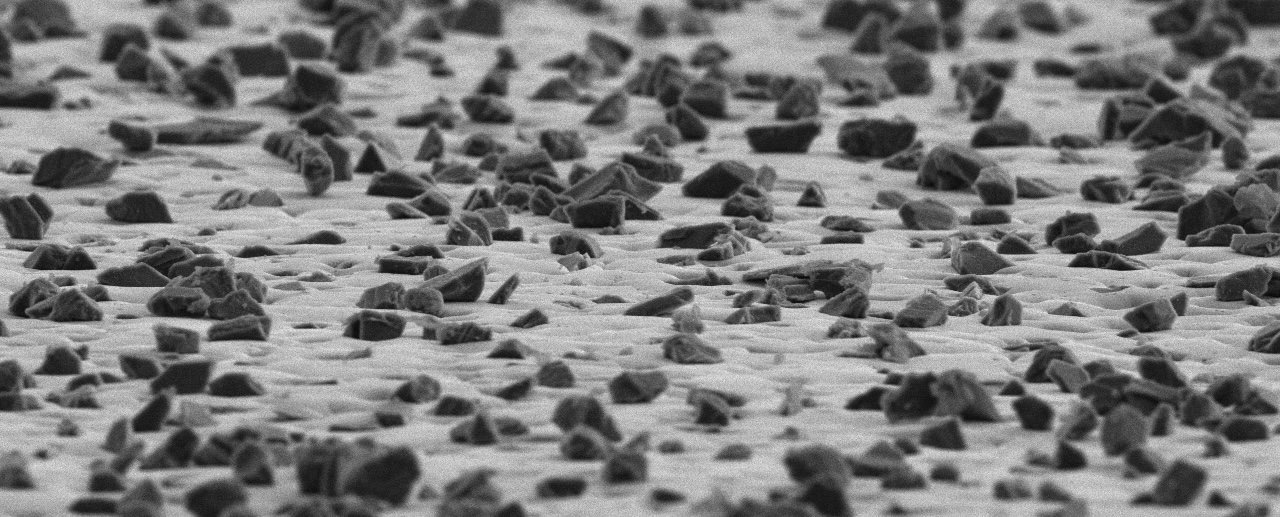